Introducing a new method to improve irrigation systems
"Thousands have lived without love, not one without water." - W.H. Auden
One of the essential aspects of successful agriculture is proper irrigation planning. One of the
key elements in
irrigation planning is measuring or monitoring soil moisture. Various devices, such as
tensometers, gypsum blocks, and
other soil moisture measuring tools, can be used to measure soil moisture. However, the results
of recent research
suggest that the combination of the sensors can reduce agricultural water consumptions greately.
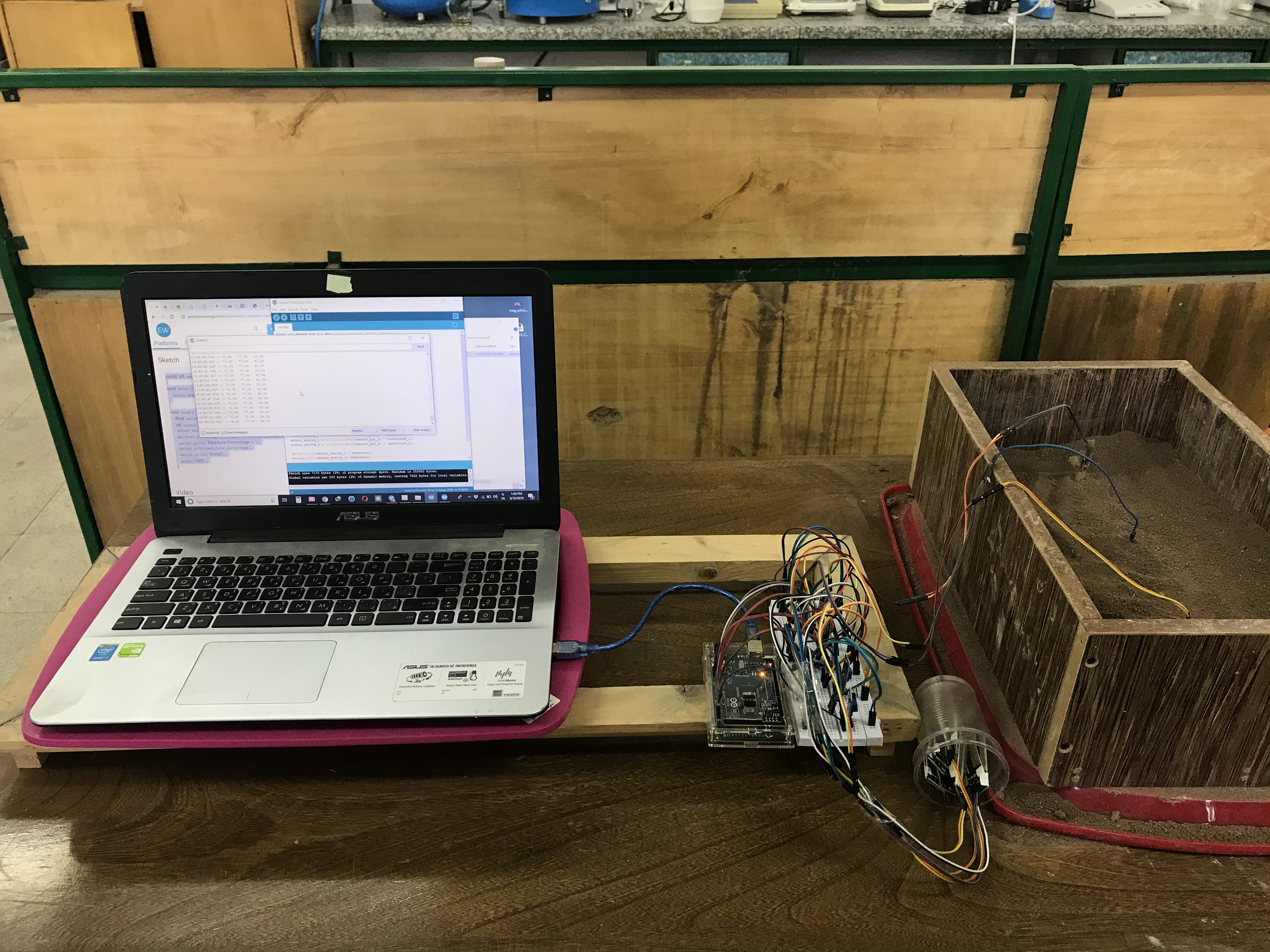
This project was initiated with the aim of developing a new type of sensor that could improve the performance of existing soil moisture measuring devices. The proposed sensor would be a combination of gypsum blocks and YL-69 sensors, which would allow for more accurate and reliable measurements of soil moisture content. By compounding these two sensors, the project team sought to leverage the strengths of both technologies, with gypsum blocks providing a porous material to absorb moisture from the surrounding environment and YL-69 sensors converting the changes in moisture levels into electrical signals that can be read and analyzed.
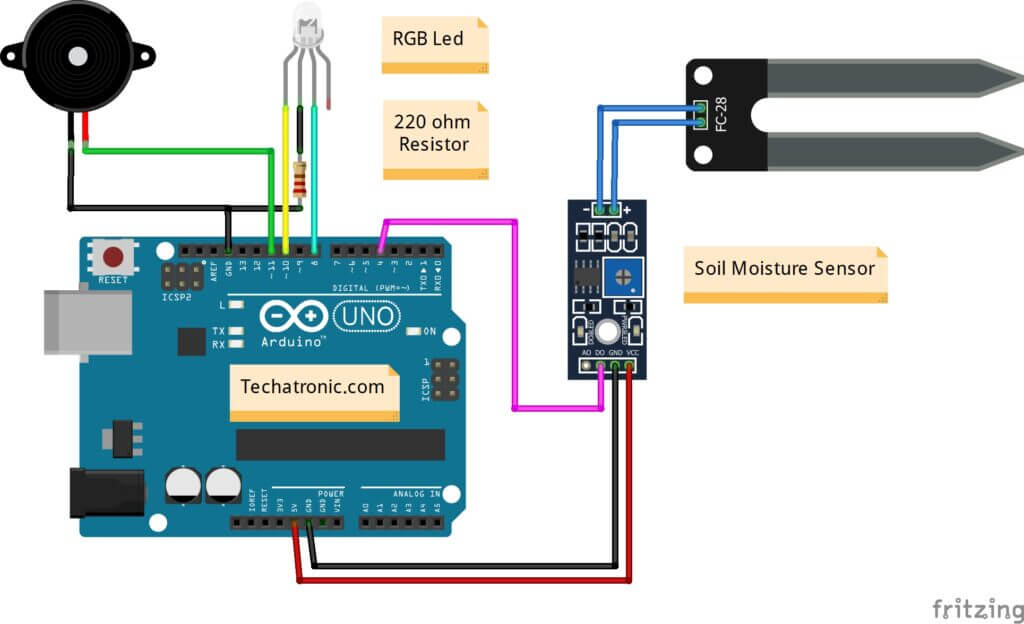
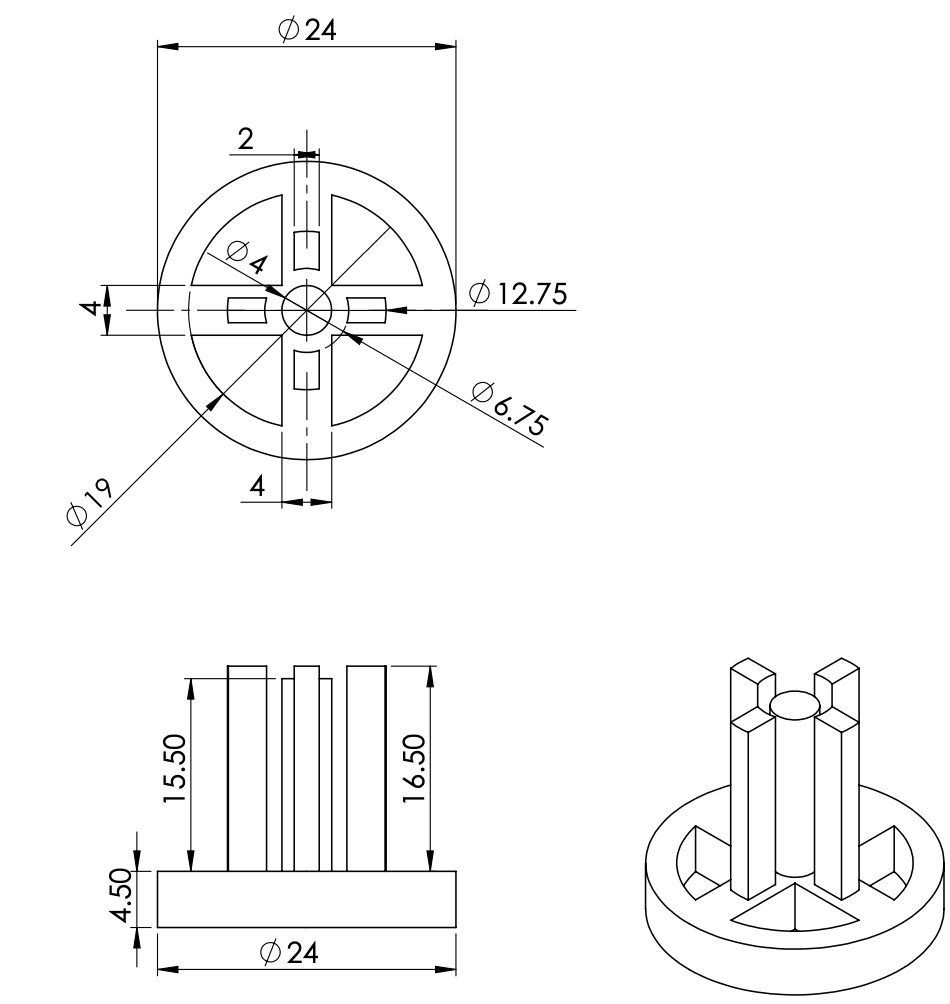
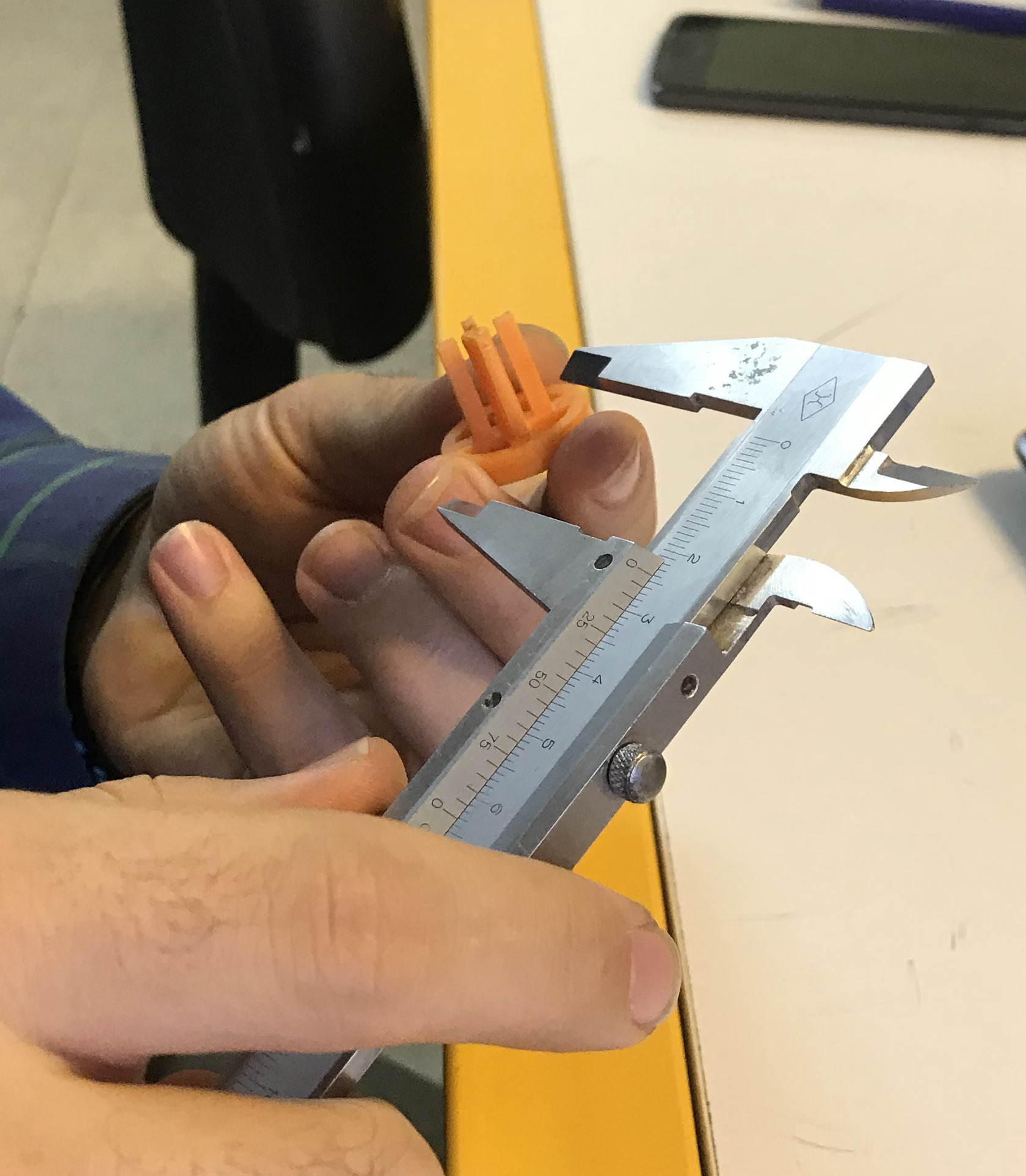
In conclusion, this project was aimed at developing a new sensor by compounding gypsum blocks and YL-69 sensors to enhance their performance. By leveraging the strengths of these two sensors, the project team sought to address the limitations of existing soil moisture measuring devices and provide more accurate and reliable data for efficient irrigation planning. Through various experiments and tests, the team was able to successfully develop a new sensor that can provide more precise and reliable data at a lower cost.
The team recognized that collecting data from the sensors was only the first step in optimizing irrigation efficiency. They needed to be able to use this data to control irrigation in real-time and make decisions based on the data collected. To achieve this goal, the team developed a server and application for users to access and control their irrigation system. The server would collect data from the sensors and send it to the user's application, which they could access from their smartphone or computer. The user could then use this data to make informed decisions about when and how much to irrigate their crops. The application had several features, including real-time updates of soil moisture levels, alerts when soil moisture levels fell below a certain threshold, and the ability to adjust irrigation settings remotely. With these features, farmers could monitor and control their irrigation system from anywhere, at any time, maximizing efficiency and minimizing water waste. Overall, the second phase of the project focused on creating an end-to-end solution that could automate the entire irrigation process. By combining the sensors with a user-friendly application, farmers could achieve optimal irrigation efficiency, saving water and improving crop yields.
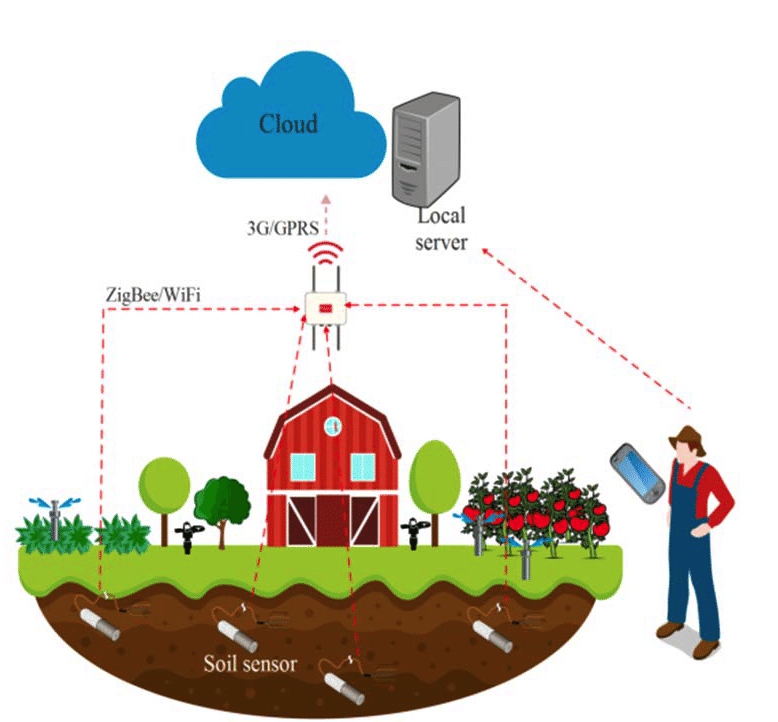
The project started by designing and manufacturing the gypsum block sensor, which includes two concentric cylindrical conductor axes as the cathode in the center of the system and plaster filling the surrounding area. The gypsum block sensor was then tested to determine its accuracy. Next, the YL-69 moisture sensor was connected to an Arduino processor to measure soil moisture levels. The project team wrote code to process the numbers read by the YL-69 sensor and establish a relationship between voltage and soil moisture. Ten sensors were defined, and their output values were correlated with humidity levels. A calibration coefficient of 1 was initially used. A threshold value was also specified to determine the irrigation period. If the percentage of moisture was less than that value, a red light turned on, and the message "needs watering" appeared. Otherwise, a green light turned on, and the message "no need to water" appeared.
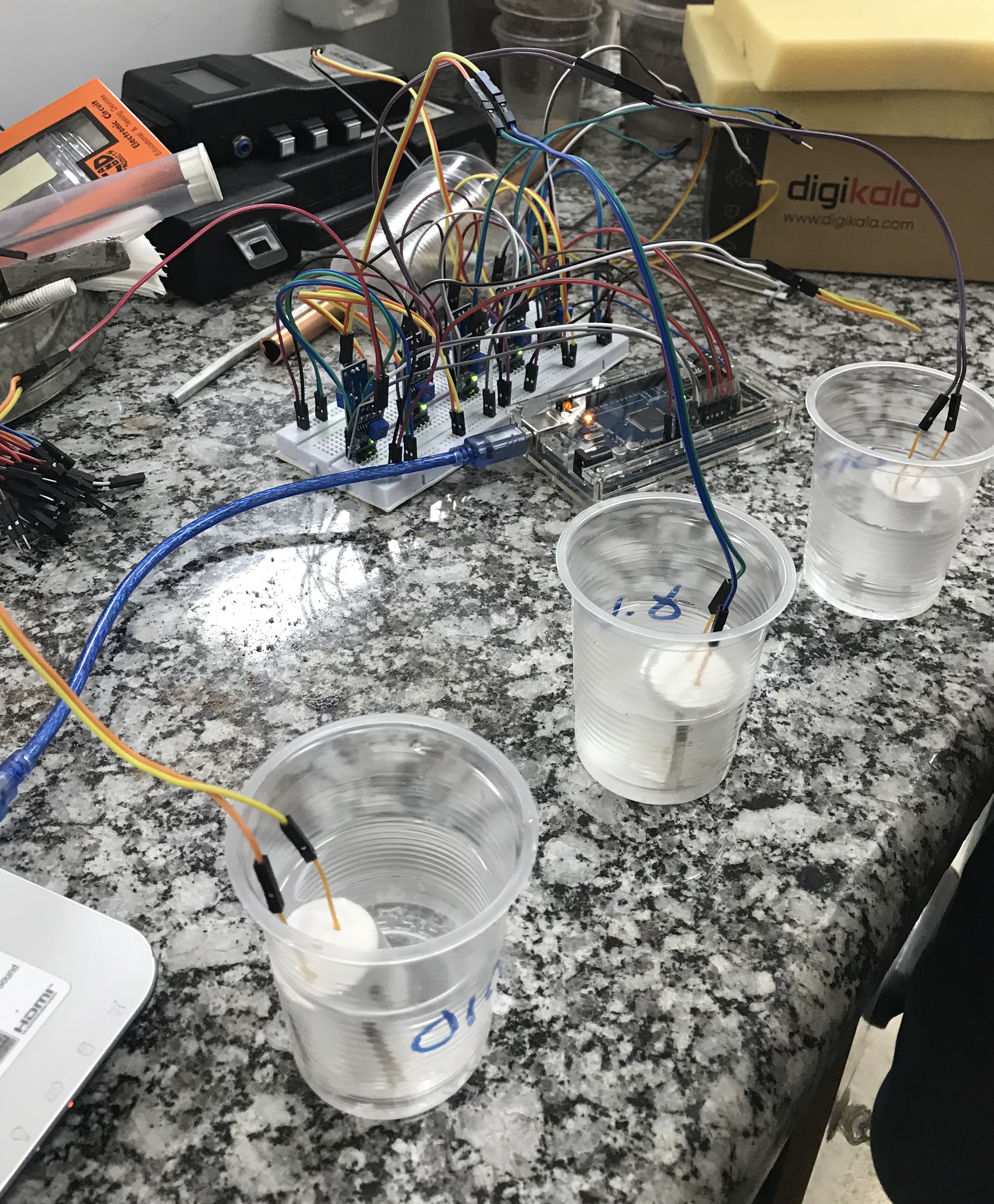
The project resulted in the successful creation of a new sensor by compounding gypsum blocks and YL-69 sensors, which enhanced their performance. The team was able to automate the irrigation process using these sensors and the data they provided by creating a server and application for users. By measuring soil moisture accurately, the project aimed to reduce agricultural water consumption and increase crop yields. The project team conducted tests using manufactured plaster blocks and found the accuracy of their measurements to be satisfactory, with a result of nearly 92%. The Aruino was used for the analysis without using the YL-69 device, and it was successful. Overall, the project provided a practical solution for farmers to monitor soil moisture levels and make informed decisions about irrigation, leading to increased crop yields and reduced water consumption.